land
Building the British Army’s Boxer: WFEL’s new MIV facility
In May, UK defence contractor WFEL opened a new production line in Stockport that will handle the production of some of the UK’s new Boxer Mechanised Infantry Vehicles, which will form a core part of the future of the British Army’s armoured capability. Harry Lye speaks to the company about its new facility and how you build an armoured vehicle.
Known for producing military bridges, WFEL, a subsidiary of Krauss-Maffei Wegman (KMW), was contracted by Artec, a consortium of KMW and Rheinmetall, to produce the UK’s 500-plus Boxer vehicles alongside Rheinmetall BAE Systems Land.
WFEL’s slice of the workshare includes fabricating hulls, assembling finished vehicles, and integrating and testing finished vehicles. The company tells Global Defence Technology that its extensive integration work, including building its military bridges and work with specialised launch vehicles, gave it a solid base to launch into the production of the Boxer.
The company has invested millions of pounds in the new production facility to produce the vehicle, plus technology transfer programmes and specialist skills such as armour-plate welding and vehicle assembly. To that end, the company has expanded on its traditional precision welding skills achieving full DIN 2303 accreditation - which is needed to produce military vehicles.
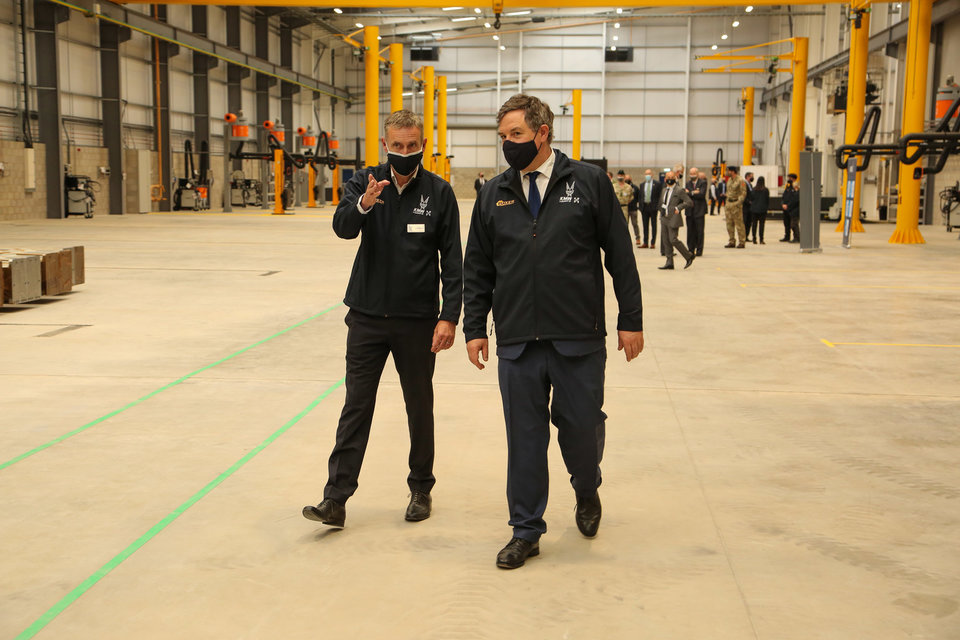
// WFL has invested millions of pounds in the new production facility to produce the Boxer MIV. Credit: WEFL
At its new 5,700m2 production facility WFEL will not only be able to produce welded elements for the vehicle but also convert the vehicle hull from a metal shell into a fully equipped and functional Boxer MIV.
To meet stringent quality controls, WFEL has installed a new coordinate measuring machine that can measure tolerances down to 10 microns. Bespoke manipulators specifically designed for manufacturing Boxer hulls have been commissioned and are ready to start production.
Commenting on the new production facility, WFEL's Boxer programme manager Simon Martindale commented: “WFEL's bespoke Boxer fabrication and vehicle assembly hall is over 5,700m2 of working space, integrated with three 25 tonne overhead cranes and with the ability to produce not only welded armoured vehicle hulls but also fully assembled Boxer MIV vehicles.
“Additionally, WFEL is upgrading elements of our existing production facility to house the specialist assembly of Boxer Mission Modules; this new facility will include specifically designed vehicle rolling road technology, to be used during the comprehensive testing of the completed Boxer vehicles."
As the facility was built during the Covid-19 coronavirus pandemic, local building contractors were granted ‘Key Worker’ status by the UK Government, allowing the facility to be completed on schedule and on budget.
Modular hulls and gearing for production
Key to the Boxer MIVs design is its modular nature. The vehicle consists of a uniform drive module and swappable user-specific mission modules that can be craned off the back of the vehicle.
Under current plans, the UK has ordered the Infantry Carrier, Command, Specialist Carrier and Ambulance variants of the vehicle. The UK is currently exploring potential lethality for the options that could see a turreted Boxer procured at some point, however, no such plans are confirmed.
In the future, the Boxer could also serve as a platform for the UK’s Mobile Fires Platform that aims to refresh the UK’s tube artillery capabilities.
WFEL told Global Defence Technology that the modular nature of the vehicle helped with its production and that the maturity of the base design increased confidence in the layout of the production facility.
The WFEL Stockport facility has been built based on lessons learned from KMW production sites in Germany that also manufacture the Boxer. WFEL’s fabrication and vehicle assembly halls have been built within walking distance of each other - something it says has enabled a leaner and more efficient facility design.
The UK Boxer MIV is billed as an advancement on the European variants of the vehicle already built for customers by KMW and the programme aims to source 60% of the vehicle by value from UK suppliers.
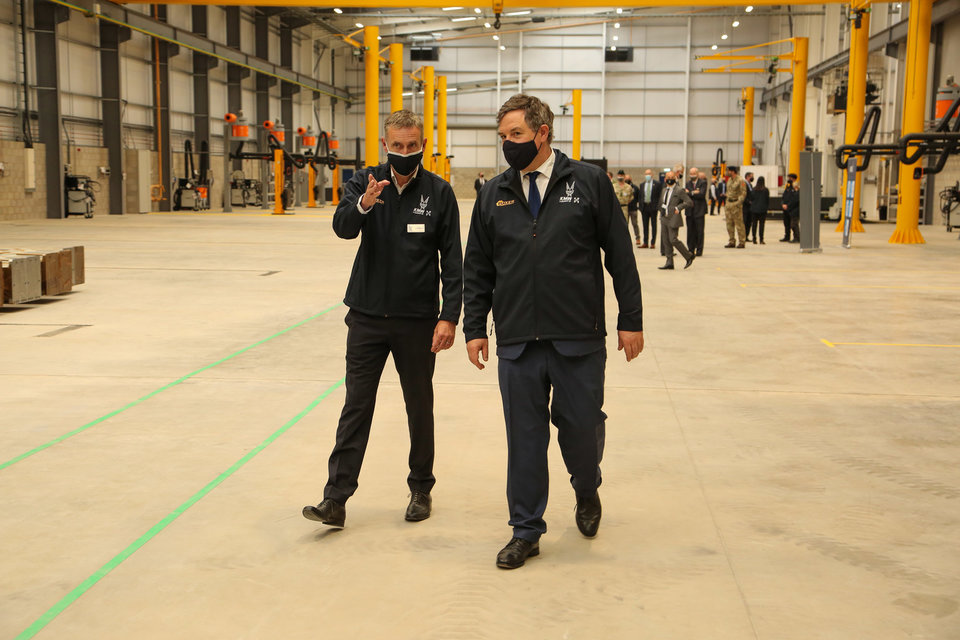
// UK Minister for Defence Procurement Jeremy Quin (R) touring new WFEL Boxer Hall during Official Opening Event. Credit: WFEL
Driving prosperity and jobs
WFEL has already taken delivery of the first vehicle components from Lancashire-based BCW Manufacturing Group and contracts have already been placed with Huddersfield-based David Brown Santasalo for 250 Powerpack blocks including transmission, engine and cooling systems.
Horstman UK has also been contracted to deliver over 250 angular gearboxes and control units for the vehicle.
WFEL has engaged in a product knowledge transfer programme to ensure the UK has access to the same design and quality documentation, production processes and equipment as European manufacturers of the Boxer do.
As the UK has not produced a new armoured vehicle for a significant time, several key skills for welding and fabricating armoured steel were not readily available and so WFEL personnel have been sent to Germany for training.
Diversifying from its bridging heritage, WFEL has hired new staff from Jaguar Land Rover, BAE Systems, Airbus, and Rolls-Royce among others to give the production a solid foundation from a skills perspective. WFEL has also employed some new staff specifically trained in different functional areas of the armoured vehicle’s production.
WFEL expects the production of the Boxer MIV to produce around 120 new jobs within the company and is currently continuing to recruit for roles associated with the programme.
// Main image: UK Minister for Defence Procurement Jeremy Quinn officially opened the WFEL Boxer MIV production facility in May. Credit: WFEL