Company Insight
Sponsored by trigalight
Innovating to make the future brighter than the past
Since its invention, innovation and sustainability have been two inextricably linked values for trigalight. The development of the illumination technology, as well as the continuous advancement of the infrastructure located at their headquarters in Niederwangen near Bern, Switzerland, has helped them reach numerous decisive milestones in the last years and greatly increased their product development capabilities.
trigalight is a brand of mb-microtec ag, a microtechnology company founded in 1969 in Niederwangen near Bern, Switzerland. mb-microtec ag is the inventor and global market leader in the development and production of this unique self-powered illumination technology that is primarily used in the tactical, watch, security, automotive, aerospace, and aeronautical industry. Around one hundred qualified employees work at the Swiss headquarters of the family-owned company, which has comprehensive knowledge in the fields of microtechnology, chemistry and physics as well as state-of-the-art infrastructure. Up to 90 percent of the Swiss made goods are exported.
The Technology
trigalight is the global leader for self-powered illumination solutions for the tactical and security industries. Per year, the brand produces over ten million light sources at its headquarters in Niederwangen. The technology consists of hermetically sealed glass capillaries, the inside of which is coated with the luminescent powder zinc sulfide and filled with tritium gas, providing reliable illumination for decades in – amongst other things – night sights and tactical watches without the need of an external energy source. While green is the color perceived brightest by the human eye, the self-powered light sources – which in their finest executions have a diameter of as little as 0.3 millimeters – come in various colors, shapes, and sizes and can be individualized to fit customer needs.
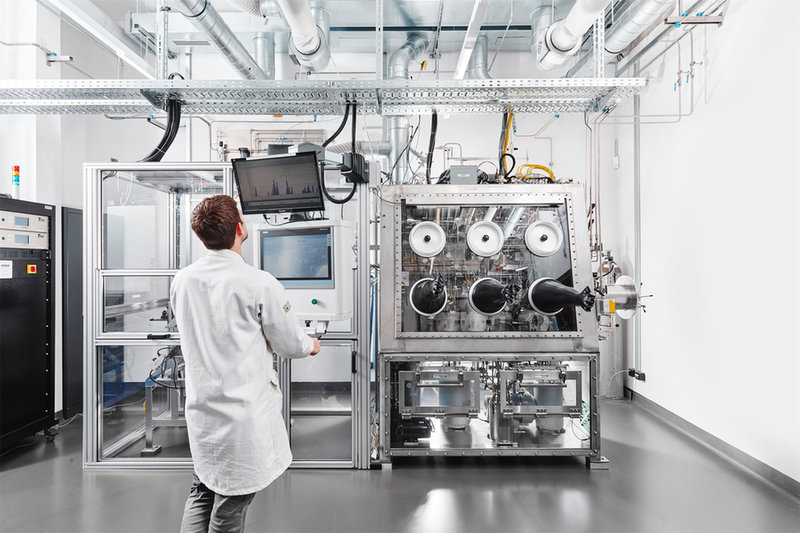
// With the help of the worlds first and only tritium recycling facility, trigalight can recover over 90% of the tritium not utilized or left behind in old products.
The Need for Innovation
The production of the tritium gas filled glass capillaries takes place within a unique infrastructure. This infrastructure has curated continuous innovation to build upon trigalight’s status as a pioneer in the industry, and helped drive the development of the technology forward. As part of their strive for innovation, the team in Switzerland has successfully developed and launched production equipment that has enabled safer and more sustainable production. Furthermore, new working structures and agile processes have reduced development times significantly while allowing for innovations to be targeted more specifically towards their customers’ needs.
As a company with a high degree of vertical integration, trigalight’s work processes can be completely mapped out internally all the way from the first idea to the practical application. To align these internal processes with external customer needs, a product-development team was newly created. This team consists of new personnel with new responsibilities and draws inspiration from concepts of design thinking to improve product quality and time-to-market. Working in shorter intervals, the team sets clearer short-term goals to speed up decision making and improve its adaptability to market trends.
Complementing these new work processes are the capabilities of the team’s Polyjet 3D printer. This state-of-the-art technology allows the product-development team to produce and test new applications more quickly, running them through a series of reality checks and trial-and-error tests to speed up their way to market readiness. While the size of the investment reaches a mid-five-figure sum, the payout has surpassed the numbers on the balance sheet by far. Instead of showing customers drawings and sketches, prototypes in different shades of gray, transparent, or full color as well as various material appearances provide a more creative, emotionally gripping, and precise exchange with customers.
Meet today's tough data security compliance and exceed even the toughest government regulatory standards with kanguru.
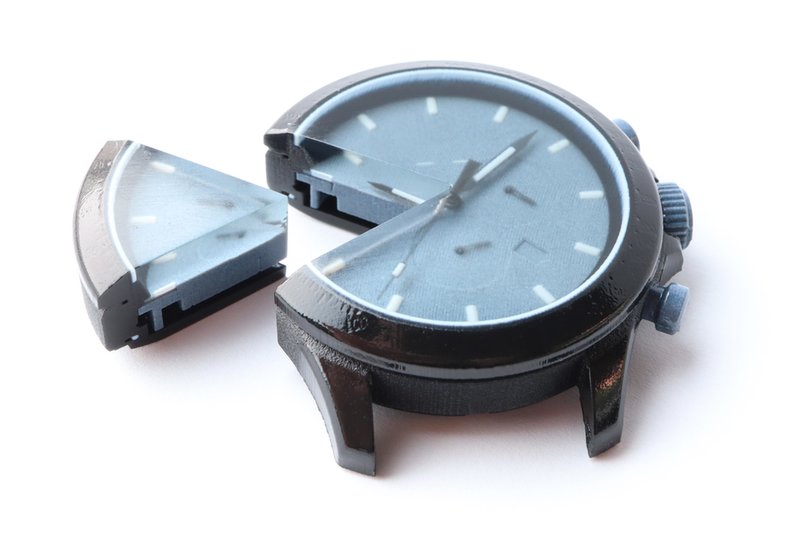
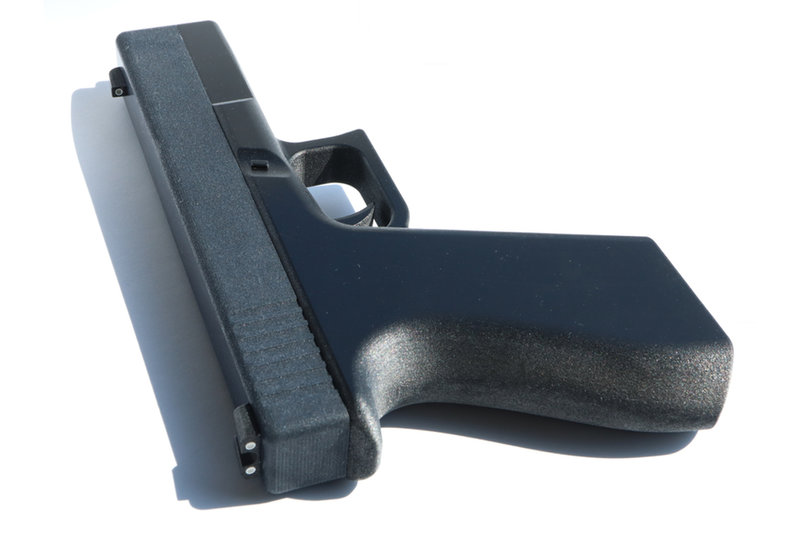
// The use of a PolyJet 3D-Printer has helped trigalight produce prototypes more quickly and make ideas more tangible for its customers.
A pioneering Spirit
The buck does not stop there: Next to optimizing product-development time and time-to-market, sustainability has been a topic of great concern for trigalight. An interdisciplinary team made up of experts in the fields of chemistry, physics, process engineering and radiation protection have worked closely with one another for over five years to successfully develop a tritium recycling facility and a tritium filling facility, the first of their kinds worldwide. Both facilities provide increased safety for their workers and the environment.
The recycling facility, which took up full operation in December 2020, recovers over 90 percent of the tritium not utilized in the final product or left behind in old products. The recovered gas is identical in quality to newly purchased tritium. This ensures that disposal of waste can be eliminated almost entirely, transportation is significantly reduced, and a sustainable life cycle is closed for trigalight products. The filling facility, on the other hand, is in the final stages of development and is set to launch in early 2023. It reduces the amount of tritium gas lost in the filling process compared to before and is a decisive factor in the mission of trigalight to protect the environment and achieve its long-term goal of zero emissions.
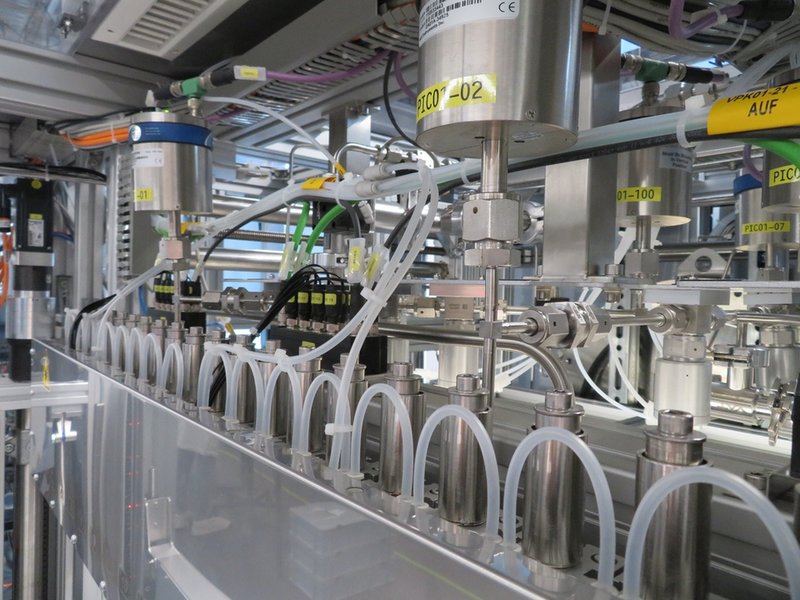
// The novel tritium filling facility increases safety, quality and efficiency of a decisive step in the production process of the glass capillaries.