air
Q&A | Maintenance
Augmented reality sustainment: Raytheon’s VirtualWorx
Getting an engineer into the field to maintain weapons systems can lead to delays and high costs. Harry Lye hears from Raytheon Missiles & Defense vice-president of sustainment and sensors John Bergeron about how the company’s VirtualWorx system aims to facilitate remote maintenance support.
Getting an engineer to the field to maintain weapons systems can cause delays and high costs. Harry Lye hears from Raytheon Missiles & Defense vice-president of sustainment and sensors John Bergeron about how the company’s VirtualWorx system aims to facilitate remote maintenance support.
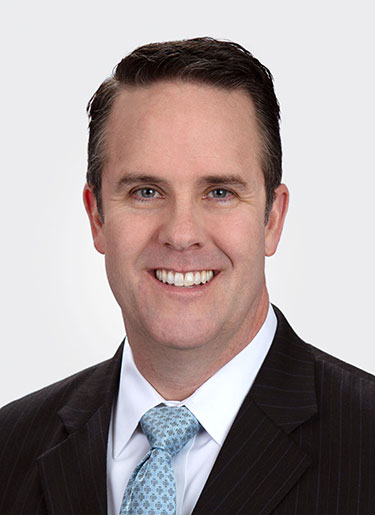
John Bergeron, vice-president of sustainment and sensors, Raytheon Missiles & Defense. Image: Raytheon
// Harry Lye:
Can you tell us what VirtualWorx is and how it works?
// John bergeron:
When we have deployed equipment on multiple platforms, if there's an issue and we have to deploy somebody, you're talking about buying a plane ticket and possibly getting a visa. That person, the subject matter expert – let’s say Sue, a 35-year engineering veteran who knows how to work on this technology - may already be deployed at a different site. And so the question is, how do we create a force multiplier for Sue or the subject matter expert, and how do we do this remotely?
The tool itself transports the subject matter expert around the world to wherever they need to be without associated travel costs and hotels, so now customers can address complex sustainment issues with subject matter experts anytime.
We provide the customer with VirtualWorx goggles that use commercial, open architecture, but are also cyber hardened because some of the equipment we're looking at has to be protected. The individual who's looking at the piece of equipment puts on the goggles, and that feed gets transmitted to the subject matter expert.
The engineer looks at their screen, and it's almost like a video game: in a first-person view, you see what the person wearing the goggles is seeing. If you've got to remove a series of bolts and you've got to do them in a particular order, Sue can physically draw lines on the screen that you can see in the googles, if you’re doing the maintenance.
You can get specific instructions; for example, if you have to read a barcode or a serial number for documentation purposes, you can do that. Sue could give you direction on the sequence of events and how to go about replacing parts.
Are there any examples of VirtualWorx in use in the field?
We've used it in cases with Patriot and the Ku-band radiofrequency system (KuRFS). There are 17 countries currently using Patriot and we've got VirtualWorx deployed with a couple of them.
With KuRFS, which looks at incoming mortars, it is quick to set up. Within thirty minutes you can defend yourself against drones, mortars and rocket artillery. We deploy the VirtualWorx system with them so that we can get instantaneous support out to the field through a virtual environment.
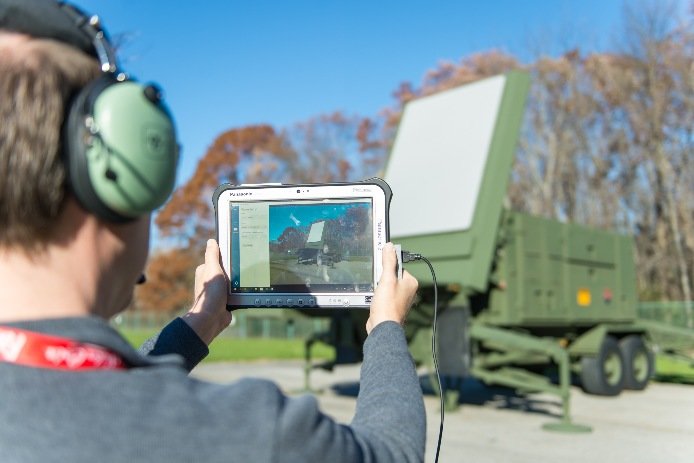
An example of the VirtualWorx system being used in the field. Image: Raytheon
I imagine customers like having quicker access to experts?
From a customer's perspective, the time constraints of traditional maintenance can be incredibly troubling. Sue can move from country to country, location to location, in a matter of minutes, as opposed to deploying around the world. The other positive is that for documentation purposes and from a knowledge transfer perspective, you can record what you've done and bring that information back into the field. You can show it to the engineers who are designing the next generation system, and they can fold that into improvements in the product.
In the case of Lower Tier Air and Missile Defense Sensor (LTAMDS), we are taking the lessons learned from Patriot, but we're also rolling out VirtualWorx with LTAMDS to help sustain it.
It's got tremendous applications. Long term, the end goal is that anytime we sell something to just ship VirtualWorx with it, as the hardware isn't that expensive. That way, when the customer has an issue, they can just give us a call and say: "Hey can we turn this thing on, I'll put on the goggles, and we'll go to work?"
How do you handle security concerns, for example, sensitive information being transmitted through a user’s goggles?
On the cyber hardening front, there is a lot of concern about the information that is transmitted, and so the work that we've done with our cyber team has been tremendous.
ITAR continues to be one of our most significant challenges, but we are well on our way to resolving that. We also have a capability where we are can limit the field of view through the goggles so that if I'm looking at a computer that's sitting on my desk, I don't inadvertently capture information that I didn't intend to transmit.
I just don't think that can be underestimated. You can imagine that this has got applications in a lot of different scenarios whether you are limiting the field of view or you're limiting the amount of information that's being transmitted. This is important because when you are talking about classified systems, it is a requirement in many cases.
Has Covid-19 accelerated interest in systems like this?
Covid-19 is something everybody continues to wrestle with, but what it has done, inadvertently, is accelerate acceptance and adoption of technology. At Raytheon we have 100,000 people working from home, we have suppliers who, understandably, when Covid-19 numbers were exceptionally high, were experiencing problems.
We shipped goggles to our suppliers to do first article inspections and helped them troubleshoot material that they were trying to get to us. Understandably, they were nervous about having our employees show up at their doorstep and potentially expose their staff, so instead, we shipped them the VirtualWorx kit, and they were able to get subject matter expertise on the supply chain side.
We are also proposing – this is early, and there is no commitment yet – to make this available to the US Navy for some of its auditing functions when they are logging physical inventory. Rather than taking a component and bringing it back to a camera, wherever that may be, they could just have somebody walk around the warehouse and look at objects. It could improve the inventory process in terms of time taken by orders of magnitude.